What to Do Before a Product Design is Locked Down
Engineers know the frustration of designing a manufacturing process that is difficult to scale up or automate. Let’s say benchtop equipment was built to test an assembly process with equipment running at a slower rate to support manual loading, and the controller and servos were selected based on that rate. But when it’s scaled up, the process does not behave in the same way at the faster production rate. It may yield unrepeatable or unreliable results. Worse yet, if the product has already been approved by the FDA then its design would already be locked in.
Making a small change to simplify the manufacturing is out of the question as it requires reevaluation. So, in the end, you’re stuck with a slow, semi-automated process that produces a garbage heap after quality assurance systems inspect everything. Clearly, it’s important to perform proper risk assessments early in process development to avoid these issues, and that’s where ATS Life Sciences Systems comes in. As an automation partner, our team of engineers can help define a reliable manufacturing process before designs are locked down.
The Risks Associated with Product Design and Manufacturing
During development, various technical, operational, and financial risks can pop up and derail an otherwise successful project.
Let’s say Marketing generates a demand forecast that, early in development, locks equipment into a manufacturing capacity. The risk here is that the demand might be slower than forecast — if it materializes at all. In this scenario, significant time and money will be wasted, especially if the product is cancelled.
The product’s designs, processes, and process times will all be in flux during development. The challenge here is that engineers will often design, build, and retool manufacturing machines, in parallel to the product development, to keep lead-times down. As a result, there is a chance that a change in the design might not be compatible with the equipment being created. The less you understand about the final process, the more risk you face. When this uncertainty becomes too great, it’s best to call in manufacturing experts to help:
- Finalize the process;
- Nail down critical-to-quality requirements;
- Optimize the process by cost and speed;
- Evaluate failure modes;
- Assess the solution’s business case and financials;
- Validate final designs.
Of course, you can’t mitigate for every risk. There will always be ‘unknown unknowns’ that can muddy your plans. In this case, assess the problem, look for solutions, and rely on expertise.
How to Identify and Prioritize Manufacturing Risks
Identifying risk has a lot to do with your experience and technical knowledge. You must learn from past mistakes and what others have done before you — successful or not. From there, engineers need to identify the requirements of the process. Ask yourself questions like:
- What does this process need to be?
- What are the requirements needed to ensure risks are understood?
- How do I clarify and assess the risk?
- What risks am I looking for?
- What inspection tools do I need?
- What is a pass/fail?
A risk heat map is a great tool during this process. It will help you understand the scope of the project, the technology involved, or if any of the subprojects/tasks are similar to what’s been done before. Make sure you take a systematic approach to create the risk heat map. You need to identify any risks in the product assembly process, technology, financial, and validation risks that can affect the project. Assess each process step in your manufacturing system and the risks they could bring to the table. For instance, it’s during this step that you might ask yourself: “How do I feed these finicky parts into this automated system?”

As for prioritizing these risks, first, focus on the issues that simultaneously have a potentially large price tag and a laundry list of unknowns. At ATS, we find these high priority concerns by assessing scope, design concept, and feeding system of each risk. We then use a quantitative scale to easily identify areas with the highest risks.
Risk Mitigation Strategies for Automation
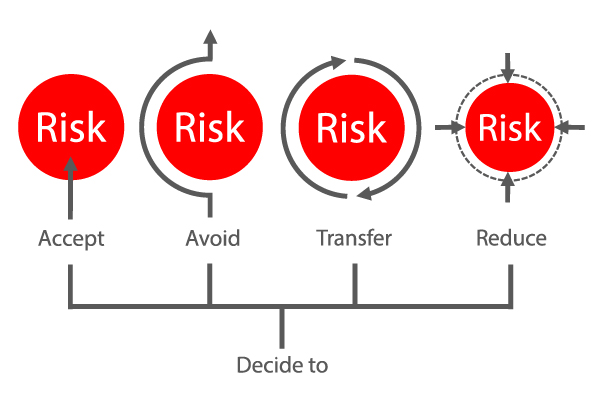
Now that you know what your risks are, it’s time to start mitigating them. Here are the 10 best practices to help:
- Design for manufacturing: eliminate production issues by keeping your manufacturing strategy in mind throughout development. Select an automation partner: ensure these experts are involved as early as possible and leverage their thought leadership.
- Coordinate with suppliers and vendors: get your supply chain on board as early as possible so they can be involved with the design, buildup, and testing of the system.
- Clarify requirements: understand the process parameters and the pass/fail criteria for each process step.
- Engineering analysis: review all drawings, ensure parts can be put together, and perform preliminary engineering tests, calculations, and assessments to estimate:
- Cycle time
- Accuracy
- Reliability
- Vibration
- Thermal stress
- Sheer stress
- Fluidic flow
- Any other critical process parameter
- Proof of Principles studies: use benchtop, pilot, full-scale models, and/or third parties to collect samples and data to prove the feasibility and reliability of the system.
- Design of experiments (DoE): assess the design space to determine which variables have the strongest effect on success; then take the first steps toward optimization.
- On-site assessments: look at current processes, the space where the final equipment will be located, and test current equipment to discover more questions, unknowns, and preferences.
- Run simulations to determine:
- Cycle times
- Robot reach
- Feasibility
- Throughput
- Bottlenecks
- Areas to optimize
- Buffer sizes
- Quantity of operators
- And more…
- Product redesigns: Consult with your key stakeholders and partners to evaluate the proposed changes to the design, assess if they are mission-critical or features of a future model, and addressable before launch.
When it’s all said and done, your final report may include a residual risk assessment. Based on the results, you can prove something is successful, unsuccessful, the data is promising, or that more study is needed. As a result, this is a good time to assess if your assumptions were relevant, more aspects of the design need testing, or you need more data.
The Benefits of Known, Standard Systems
Much of the risk associated with a new automated assembly is alleviated when standard equipment is used. The challenge is that typically these standardized systems lack either flexibility or throughput. Our Symphoni™ technology breaks this tradition by offering both speed and versatility.
You can use a single Symphoni module to simulate the automation process during the product’s R&D phase. Then, you can add additional modules during clinical trials as production volume increases. When the product is ready to be fully launch into the market, all these modules form the final production equipment. Engineers can also speed up product risk assessments by accessing the automation platform’s standard tools to create:
- Simulations
- Cycle times analysis
- Design of Experiments
- Engineering analysis
When you use Symphoni technology, most of your hardware and all your software is standardized so the development of the assembly system is sped up as you need only to test the system’s contact tools and software settings. As a result, you can limit your risk by using well-understood systems without compromising on speed, product variation, or precision. More importantly, production can meet market demand.