We perform complete powertrain final tests for engines, transmissions, and axles. ATS is your solution to FTT (First time through) and lower product life cycle costs.
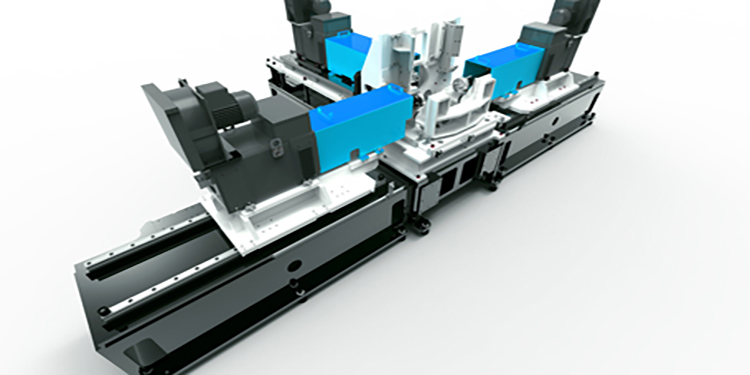
Complete Product Line of Powertrain Final Test Solutions
We supply the proper application and use of both a well-designed IPV (In Process Verification) process in conjunction with a world class final test strategy. This will be a major contributor to the OEM FTT and lowering piece price by significant cost of quality avoidance.
We will work wit your product development team to design a quality process so that you achieve the highest product quality for you product and get the most efficiency out of your capital investment.
Engines
- Engine Cold Test
- Engine Production Hot Test – Loaded
- Engine Production Hot Test – No Load
Transmission
- End of Line Leak Test Final Function Test
- End of Line Function Test and NVH (Noise Vibration Harshness) Test
- End of Line NVH Test
Axles
- Function Test
- Noise Vibration Harshness (NVH) Test
- Balancing Test
Engine Cold Test
Engine Cold Test machines verify that the engine assembly process is in control, and that a quality product is being produced. Usually we use a fully automatic machine that tests engines delivered on an assembly pallet from a conveyance system. This method of testing does not require coolant or fuel to be delivered to the engine. The engine only needs to be filled with oil to the proper operating level.
Therefore an engine does not have to be “fired” for a very detailed test to be performed, hence the name “cold test”. ATW was the originator of this technology in the 70s and has since evolved our product offering to the most recent technologies available. The revolution in light vehicle ice (internal combustion engine) cold test technology has allowed almost all global OEMs to eliminate the need for production hot test. Generally speaking, a modern cold test can find engine defects better than actually running the engine via Hot Test.
How It works
The engine is clamped up automatically and a variable speed drive spins the crank shaft at various speeds. A computer acquires high speed analog data from torque and pressure transducers mounted on the machine. Data is also collected from cam and crank sensors mounted on the engine. The collected data is analyzed using special algorithms and limits are applied to the results calculated from the waveforms to determine the accept/reject status.
Typical engine defects that can be found:
- Cam-Crank timing
- Excessive vibration
- Exhaust valve opening/closing positions
- Ignition coils
- Intake manifold leaks
- Intake valve opening/closing positions
- Leaky head gasket
- Leaky intake and exhaust valves
- Missing can/crank bearings
- Missing piston rings
- Oil pump/relief valve
- Spark plug gap
- Variable valve timing actuator/solenoid
Engine Hot Test – Loaded
Loaded (put a well-controlled load on the engine during running) Hot Test is used today primarily in large diesel market, where horsepower verification and fuel consumption calibration can only be done while running the engine.
How It Works
This method of Hot Test starts an engine using fuel and there is torque load applied to the crank shaft while the engine is running. Engine coolant is required for this type of testing and an eddy current dyno is typically used to apply the load to the crank shaft. A Loaded Hot Test machine can be a fully automatic test station that tests 100% of engines manufactured or can be configured as a semi-automatic audit machine that only tests a small percentage of the production volume.
The engine is clamped up manually or automatically depending on the type of machine. After the engine is clamped, the computer system controls the machine to start the engine and command speed and torque loads. The computer system also communicates with the Engine Control Module (ECM) to monitor status and error codes generated by the ECM. Data is acquired continuously during the test and is compared to limits to determine accept/reject status. Test duration can vary from a couple of minutes to 10 hours depending on customer requirements. The Flight Recorder feature of our software provides an easy graphical method for reviewing the complete data record after testing has been completed.
Typical engine defects that can be found:
- Coolant system pump/thermostat
- Defective engine sensors
- Defective ignition coil
- Defective wiring harness
- ECM error codes
- Horse Power and Torque
- Incorrect engine timing
- Visual inspection for oil and coolant leaks
Engine – No Load Hot Test
No Load (free running engine) Hot Test is primarily used for engine start verification prior to shipment to avoid costly final assembly plant warranty issues. Also knows as “turn and burn” tests, these stations are often used as a confidence test for the quality process, and also act a a low cost electrical test. Often operator subjective, an NVH test looking for odd engine noise may also be used in this test, as well as for fuel rail leakage using phosphorus in the fuel.
How It Works
This method of Hot Test starts an engine using fuel and there is No Torque Load applied to the crank shaft while the engine is running. Depending on how long the engine is allowed to run, engine coolant might be required. A No-Load Hot Test machine can be a fully automatic test station that tests 100% of engines manufactured or can be configured as a semi-automatic audit machine that only tests a small percentage of the production volume.
The engine is clamped up manually or automatically depending on the type of machine. After the engine is clamped, the computer system controls the machine to start the engine and collect data from machine and engine mounted sensors. Data is acquired and compared against limits to determine accept/reject status.
Typical Engine defects that can be found:
- Coolant system pump/thermostat
- Defective engine sensors
- Defective ignition coil
- Defective wiring harness
- Incorrect engine timing
- Visual inspection for oil and coolant leaks
Additional Information
Battery Design Authority – What 90 Battery Lines Have Taught Us
Watch the Webinar On-Demand >
The Tangram Issue in Battery Testing
Watch the Webinar On-Demand >
Electric Vehicle Challenges: Are You Prepared?
Watch the Webinar On-Demand >
Discover The Key Element: EV Battery Testing,
Watch the Webinar On-Demand >
Hear What the Experts Have to Say on EV Battery Assembly.
Watch the Addressing the Battery Challenge Webinar >