By: Andrew Glaser | VP, Global Sales, ATS Life Sciences
An old manufacturing metric (TEEP) is very relevant when it comes to high speed automated assembly Total Effective Equipment Performance (TEEP) is an uncommon but powerful manufacturing metric that is both broader and more revealing than the widely used Overall Equipment Effectiveness (OEE). The difference between TEEP and OEE is simply that OEE measures equipment effectiveness over scheduled operating hours, whereas TEEP measures equipment effectiveness over available calendar hours (24 hours per day and 365 days a year = 100% TEEP utilization). TEEP reports the metric for the “bottom line” effectiveness of assets by taking into account Utilization. Table below shows how TEEP compares to other metrics and illustrates how it incorporates Utilization.
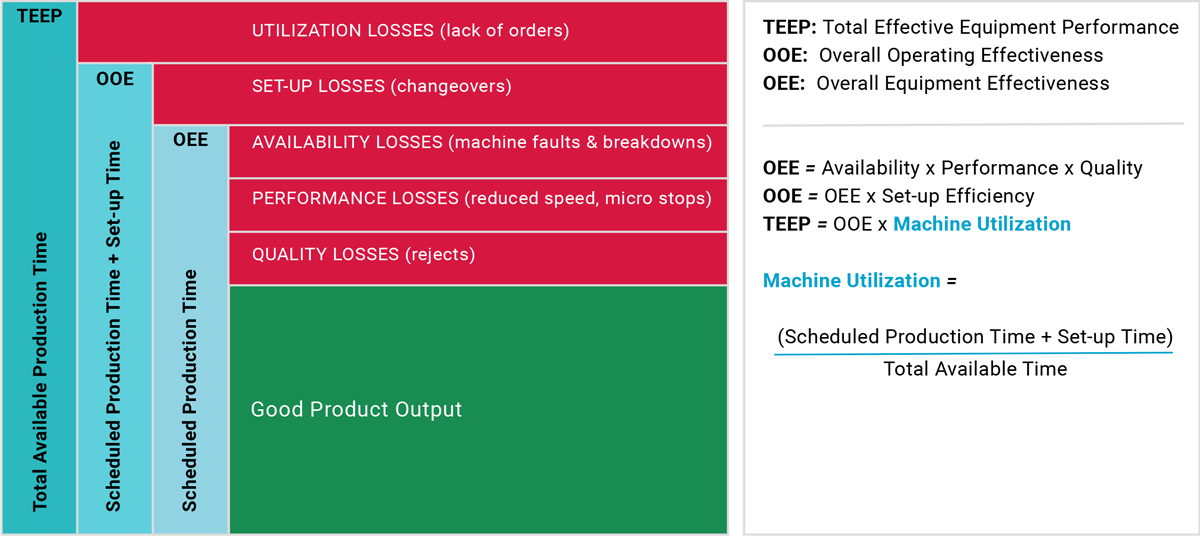
Utilization of an asset is critical in manufacturing and especially in the realm of automation in order to meet customer demand, meet internal financial targets, and recoup the capital investment. Yet in many cases, asset Utilization is either overlooked or assumed to be a factor beyond operational control, perhaps because it depends on incoming sales orders. That is, if there are orders that a machine can fulfill, the machine is placed into operation and its performance evaluated by OEE. On the other hand, if there are no orders, the machine sits idle. Utilization and TEEP both drop, but why care if nothing can be done about it from an operational perspective?
Low Utilization is particularly common in low-mix, high-volume (LMHV) production environments. Manufacturers in such industries have long invested in “hard automation” technologies such as “continuous motion” because (i) it makes no sense to apply manual labor to scale up to the required capacity to meet demand, and (ii) the asset (machine) will do one thing really well and at high speed to produce a single product type. Although these technologies meet the need of high volume, their single-purpose dedication results in suboptimal Utilization, particularly when measured over the life of the asset. The graph below illustrates the problem by comparing Machine Capacity to a typical product life cycle curve.
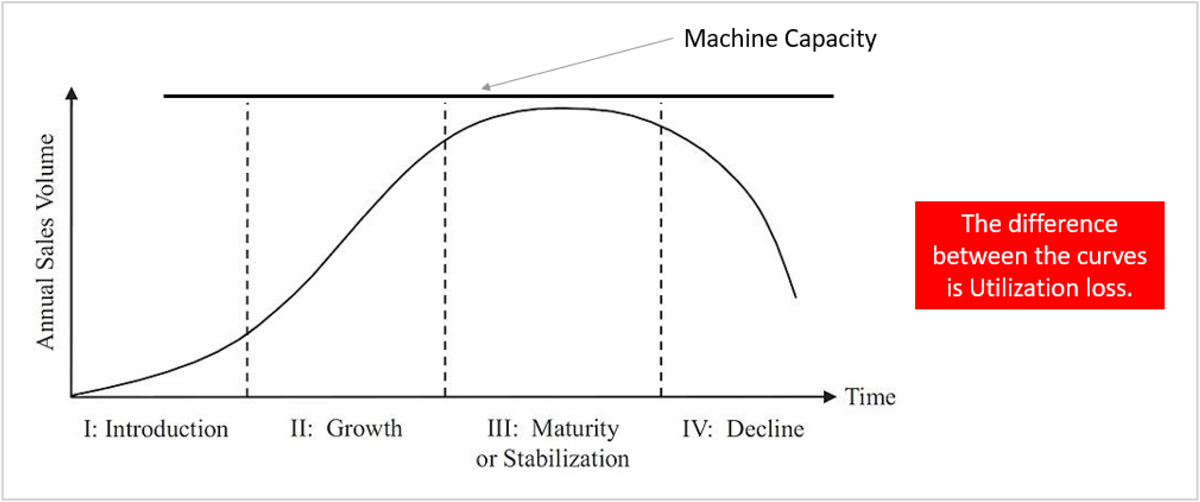
The good news is that with the introduction of assembly technologies that combine high speed and multi-product versatility, LMHV environments can now be transformed to high-mix, high-volume (HMHV) environments. These new technologies permit the deployment of multi-purpose assembly machines. That is, they result in machines that have the versatility to run multiple products with quick changeover. This means that these machines are no longer condemned to the low Utilization that characterizes single-purpose machines. Instead, when there are no orders to run Product A, they can be quickly changed over to run Product B (or C or D or E, depending on how many products they are tooled to run). Thus, these machines can effectively run all the time, rather than only when there happens to be orders for one particular product. This results in additional productive capacity – measured by a higher TEEP – that yields more revenue and more profit from the asset!
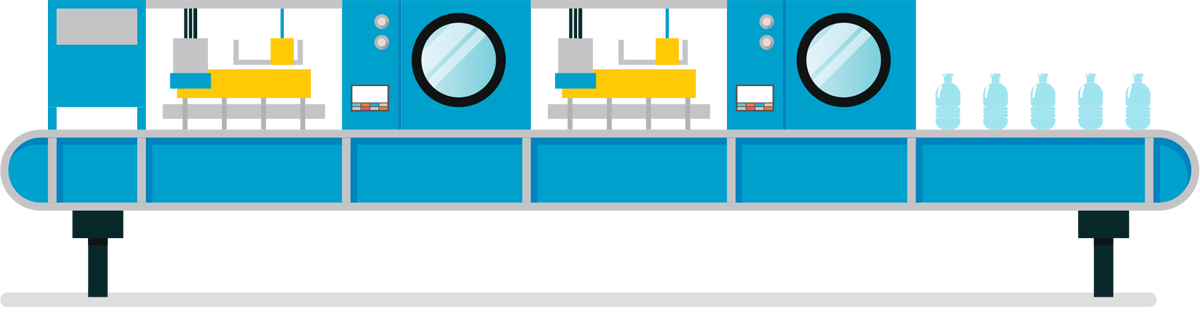
Multi-purpose assembly machines overcome the TEEP-diminishing conditions that plague dedicated, single-purpose machines such as:
- Slowing in demand that prevents the asset to be utilized because the machine cannot be adapted to produce alternative products (i.e. costly or impossible to changeover).
- Demand completely shuts off and the machine is idle. The machine collects dust and can be depreciated but it’s not utilized.
- The opportunity cost that requires the manufacturer to purchase an additional machine to meet some new demand even though the dedicated machine remains underutilized for the aforementioned reasons.
- A manufacturing strategy that does not plan for contingencies in how an automation asset can be utilized to its fullest and over its useful life.
Want to learn more?
- Email us at SymphoniTech@ATSautomation.com
- Sign-Up for our Quarterly Newsletter.
- Connect with us @SymphoniTech on LinkedIn, YouTube, Twitter and Facebook.