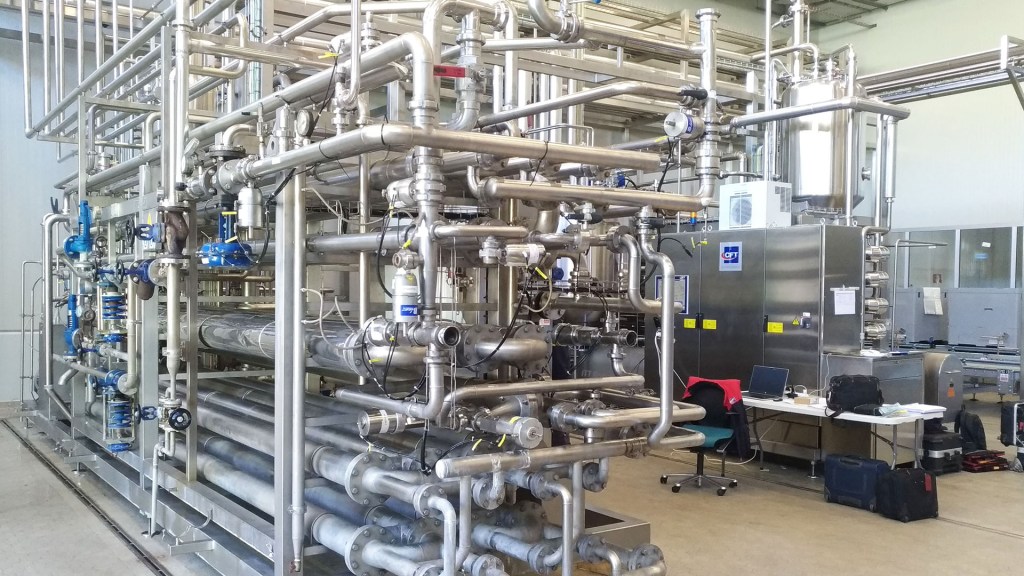
Apple purée production plants for Vog Products
CFT Group and Vog
One of the CFT Group’s historical clients is based in the town of Laives, in the province of Bolzano: Vog Products.
Vog is an innovative, cutting-edge company in the fruit processing sector (in particular apple purée production plants) and works in collaboration with all the fruit cooperatives in Trentino-Alto Adige. In practice, this means that most of the apples in the region are processed by Vog, along with other types of fruit.
Vog and CFT Group have known each other for over 20 years. The first apple purée production plant that they had installed in fact dates back to 2000 and was a true success: the two companies discovered that they shared the same passion and attention to quality and productivity.
In 2018 we were again called upon by Vog, who had in the meantime changed management, for a project to expand and update their fruit purée plants. We were happy to take up the challenge once more: although we had already worked together in the past, this time it was about winning the trust of the new people running the company and the whole CFT Group team was motivated and determined to reconfirm their skills.
Productivity increase
The new board of Vog called us with the aim of increasing productivity in its apple purée production plant: this meant adding a second fruit purée line and a second dedicated aseptic filling plant, in addition to the one already up and running at the company.
Very early on however, we ran into a problem. Adding only one line with cutting-edge technology, at the end of the installation Vog would have found itself with two fruit purée plants that, although similar, had many differences between them at the same time. Separating them would have been more than fifteen years of innovation and technological development, with a notable difference in quality between the two final products. What could be done?
After discussing it between ourselves and listening to and analyzing Vog’s requests, we proposed our ideal solution.
CFT’s solution for Vog
First of all, the new state-of-the-art fruit purée plant was designed using the latest CFT Group technology for the processing of fruit either with or without stones.
The absolute protagonist in this case is the Zenith Chrono enzyme inactivation system with cold extraction, short processing time and anaerobic environment, customized for Vog with the insertion of an automatic pneumatic soda wash.
The enzyme inactivation is immediate in the Zenith Chrono, guaranteeing an optimal consistency and an output product of really fantastic quality, minimizing the consumption of ascorbic acid and conserving colour, flavour and other organoleptic properties.
The fruit purée plant already in use at Vog was not replaced, but revised, reassembled and automated: the reception part was modified and installed the same as the one in the new line and the old extractors were replaced with CFT Group’s Giubileo technology, to then skilfully integrate these new components with those that were already there.
This will allow Vog to still reap the benefits of the original investment made for several years, by running two lines in parallel that although different are still both efficient and highly productive. Having two similar but not identical lines allows Vog to also speculate a further differentiation in the products on offer in the future by proposing two different products.
In addition, to take full advantage of the potential offered by a group such as CFT, both lines have been equipped with a Raynbow optical sorter produced by Raytec (a company that is part of the CFT Group), that uses a high speed and double vision technology, able to examine 100% of the surface of the product in a very short time.
Composition of the plants
The proposed solution was enthusiastically approved by Vog and installed in a few months.
The two automated fruit purée lines are composed of:
- Reception and washing system
- Brush machine
- Raynbow optical sorter (Raytec)
- Possibility of manual sorting
- Zenith Chrono cold extraction and enzyme inactivation system
The product resulting from this line is stored in a cellar and kept at 5° until subsequent processing.
A new aseptic filling line consisting of an Olimpic 12 t/h plate sterilizer and a Macropak AF/2 filler, installed together with a tubular sterilizer and an existing CFT filler, was also supplied in a modernized area of the factory.
In this current configuration the line was completed with an articulated system of pallet transport, complete with shuttles designed and built by CFT Robotics with the aim of automating and managing the feeding of empty drums and the transport of the full drums up to the final phase in complete safety, passing through a station for the automatic labelling of every single drum and a strapping station. Today the line looks like this:
- Olimpic plate sterilizer
- Existing Olimpic tubular sterilizer
- Macropak AF/2 aseptic filler
- Existing Macropak TM2000/2 aseptic filler
- Conveyor system complete with CFT Robotics shuttles for the automated transportation of the drums
- Labelling machine
- Strapping machine
The complete satisfaction of what was done by the CFT Group convinced Vog to make the new sterilization and aseptic filling room visible through a glass corridor.
In this way the potential end customers of the South Tyrolean company can verify the cleanliness, organization and management of what is the most delicate phase in the whole production process.
The added value of CFT Group
We believe that this project is very interesting for at least two reasons: it confirms the quality of the CFT Group technologies and innovations, also demonstrating our ability to offer customized solutions, artfully tailored to the customers’ needs. In some cases, as it was for one of Vog’s fruit purée lines, it becomes necessary to be able to design “hybrid” systems, where new technology is perfectly integrated with that which is already installed, improving it. Thanks to the experience, variety and quality of the solutions, CFT Group is without a doubt an ideal partner for this type of projects.
Market prospects*
The fruit purée market is poised to hit $14,549.8 million by 2023, with an impressive average growth rate of 4.4%. Europe will be one of the areas with the highest growth rate.
The CFT team for this project:
- William Dattaro – Sales Area Manager
- Manuel Gonizzi – Project Manager
- Andrea Malvisi – Project Manager
*Source: marketwatch.com